2) Improve the forging and spheroidizing annealing process, eliminate the network, ribbon and chain carbides, and improve the uniformity of the spheroidized structure.
3) After machining or cold plastic deformation, the mold should be subjected to stress relief annealing (>600℃) before heating and quenching.
4) For molds with complex shapes, asbestos should be used to block threaded holes, dangerous sections and thin walls should be wrapped, and graded quenching or isothermal quenching should be used.
5) Annealing or high temperature tempering is required when repairing or refurbishing the mold.
6) The mold should be preheated during quenching and heating, and pre-cooling measures should be taken during cooling, and an appropriate quenching medium should be selected.
Breath collector upper cover mold
Among the best respiratory equipment available on the market is the Upper cover mould of the respirator. This type of mask is designed to keep the user cool while preventing him from breathing in toxic fumes. Its downward facing exhalation valve helps keep the lens fog-free so that the user can work without getting tired. When dealing with mold, the upper cover mould on the respirator is especially important.
Mold Name | Upper cover mould of respirator |
Product Material | ABS |
Mold Steel for cavity | NAK80 |
Mold Steel For Core | NAK80 |
Steel For Base | S50C |
Mold Estimated Size | 230X200X231mm |
Mold Weight | 60kg |
Press Machine Size | 100T |
MOQ | 1 Set |
Trade Terms | FOB |
Payment Terms | 50% prepayment before design making, 50% payment after final sample is confirmed. |
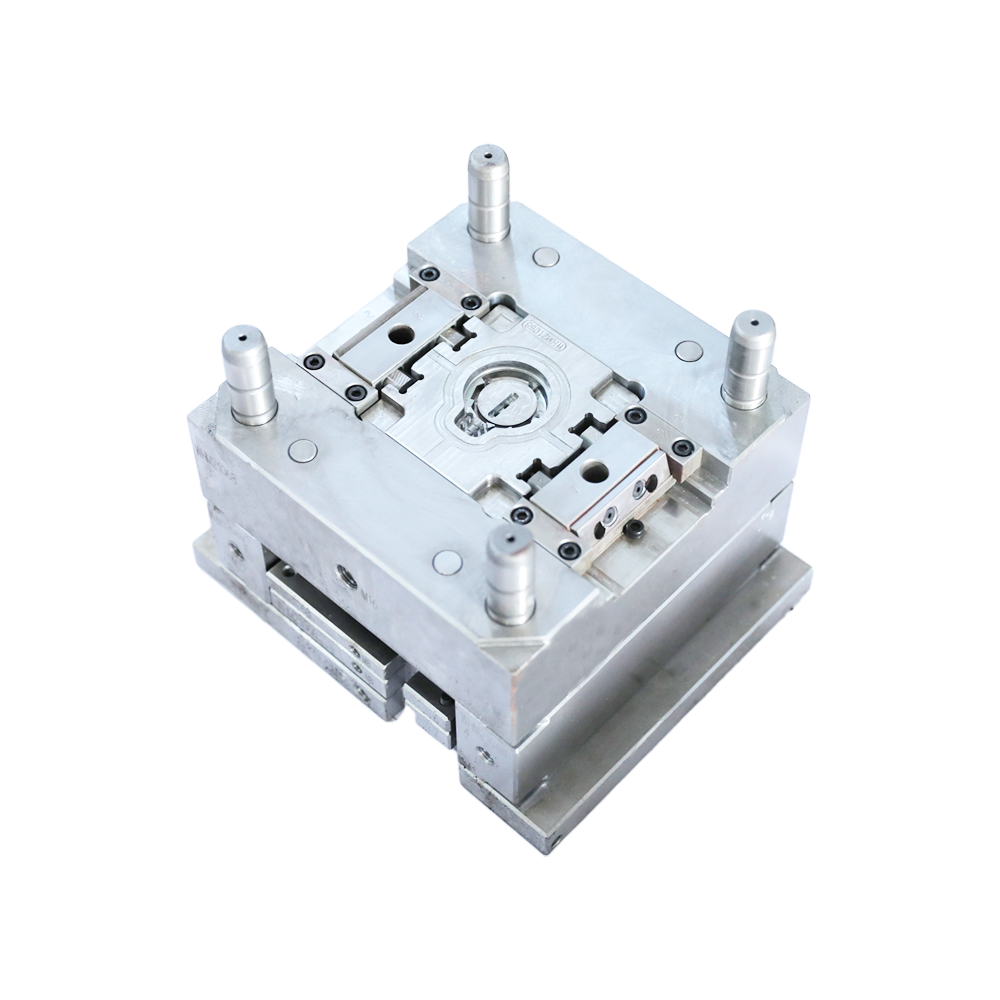
7) The quenching heating temperature and time should be strictly controlled to prevent overheating and overburning of the mold.
8) After the mold is quenched, it should be tempered in time, and the holding time should be sufficient. The high-alloy complex mold should be tempered 2-3 times.
9) Select the correct grinding process and suitable grinding wheel.
10) Improve the mold EDM process and perform stress relief tempering.